Physical Properties of High Speed Steel
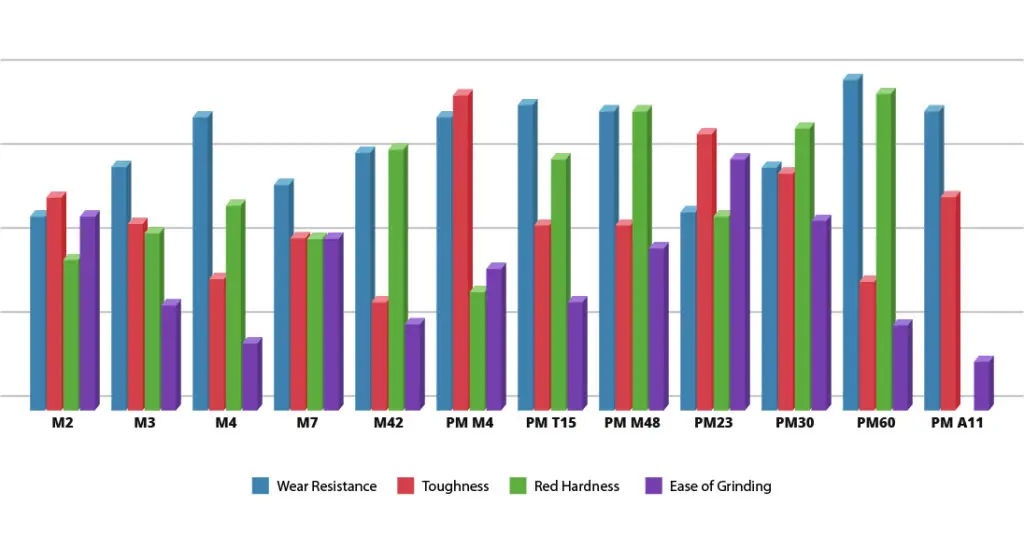
High speed steel is a class of tool steel alloys used for high-speed applications such as cutting and drilling. Understanding the physical properties of high speed steel will help you to find the right choice for your application.
Molybdenum HSS Steel Alloys
The molybdenum series of high speed steel grades is considered the default option for many tool steel applications. Five common M-series grades include M2, M3, M4, M7 and M42.
- M2: This is the most popular choice among tool steels. It provides a balance of wear resistance, toughness, red hardness and ease of grinding. There is more on M2 below.
- M3: This grade has higher carbon and vanadium levels compared to M2 (though lower than M4). The result is improved wear resistance and red hardness but decreased toughness. Ease of grinding is substantially decreased compared to M2 (by about half).
- M4: With even higher carbon and vanadium levels than M3, the characteristic changes of M4 are even more extreme. Wear resistance and red hardness are increased compared to M3 while toughness and ease of grinding are decreased.
- M7: With increased molybdenum levels compared to M2, this grade can offer highly balanced characteristics. It has highly balanced toughness, red hardness and ease of grinding as well as elevated wear resistance. All four characteristics are about average for the M series.
- M42: This HSS steel grade has elevated cobalt levels. It is characterized by high wear resistance and red hardness but very low toughness and ease of grinding. It is popular for metal manufacturing.
Properties of Molybdenum High Speed Steel – AISI M2
This grade of molybdenum HSS steel deserves special mention because it is by far the most popular. Previously, that honor went to the T1 grade, a type of tungsten steel. However, M2 has superior bending strength, toughness and thermo-plasticity. This is no small improvement. Each characteristic is increased by at least 50% over T1. M2 offers an excellent balance of cost and performance. It is used for mills, rolling racks, knives, drills, taps, dies and many other applications.
Tungsten High Speed Steel
The T series and M series high speed steels are the two major types containing varying amounts of tungsten. PM T15 has higher tungsten levels than other grades at 12.25%. This inclusion places PM T15 among the best of our high speed steel alloys for wear resistance and red hardness. Its toughness is comparable to M3, but the ease of grinding is relatively low. See tungsten high speed steel for more information and details regarding this type of steel.
Powder Metallurgy HSS Grades
Powder metallurgy uses metal powders to create steel alloys, helping to improve many characteristics. Some powder metallurgy grades include PM M4, PM M48, PM 23 and PM 60.
- PM M4: Powder metallurgy improves cutting tool life compared to conventionally wrought grades. This gives PM M4 very high wear resistance and toughness. However, the red hardness and ease of grinding are below average.
- PM M48: This grade has increased tungsten and an addition of 8.5% cobalt compared to PM M4. This improves its red hardness significantly as well as ease of grinding. However, toughness is reduced by more than a third.
- PM 23: This grade is a powder metallurgy steel corresponding to AISI M3:2. It has relatively balanced characteristics, all of which are superior to M2. In particular, toughness and ease of grinding are high.
- PM 60: This is a high-alloyed grade including high levels of carbon, cobalt, molybdenum, tungsten and vanadium. It has the highest wear resistance and red hardness of any grade but low toughness and ease of grinding.
High-Vanadium HSS
PM A11 is a powder-metallurgy, high-vanadium steel alloy. It is characterized by excellent wear resistance (higher than all grades other than PM 60) and good toughness. However, it has extremely low red hardness and poor ease of grinding.