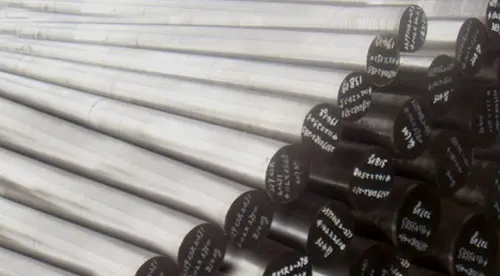
Steel has always been a popular choice for a high-performance tool metal. However, there is a subset of the hardened steel alloy that is superior for high wear resistance. It can be machined at high speeds, earning the name super high speed steel.
Significant elements of super high speed steel alloys include carbon, chromium, tungsten, molybdenum, vanadium, or sometimes cobalt in varying combinations. The addition of cobalt increases the hardness and cutting efficiency in applications where high temperatures are present.
For over 65 years, Griggs Steel has been the trusted supplier of super high speed steel to companies in the tooling and forming industries across North America. With superior customer service, extensive inventory, competitive prices and fast turnaround, we ensure that our customers have what they need when they need it, with uncompromising quality.
What Is Super High Speed Steel?
High speed steel, also called HSS, is comprised of steel clad in metal carbide. Metal carbides can be made of tungsten carbide, molybdenum or vanadium. The new structure composed of the substrate and carbide contains high carbon content and provides exceptional characteristics that exceed either on their own. Other alloys can’t offer the same structural hardness or ability to be machined at high speeds.
When tooling components that require a high degree of accuracy, using a substandard tooling steel can not only compromise the quality of the part but could lead to unscheduled downtime. Super high speed steel offers unparalleled precision, abrasion resistance and reliability in high heat, high speed and high impact use. While HSS steel is ideal for tooling, it has a tendency to get brittle at extremely high temperatures, so it is not suitable for applications where a more malleable steel is needed.
How Is Super High Speed Steel Used?
High speed steel is used in numerous cutting and forming applications, such as:
- Cutters
- Taps
- Drills
- Tool bits
- Saw blades
- Kitchen knives
- Pocket knives
- Files
- Other industrial and household tools
There are many grades of tooling steel that are perfect for high speed manufacturing applications. Two of those are M42 steel and PMT15 steel.
M42 Steel
When your goal is shorter cycle times in your high strength, pre-hardened steel manufacturing processes, M42 steel is the perfect choice for your tooling needs. This molybdenum series high speed steel alloy has an exceptional red hardness.
It has 8-10% more cobalt than others in the series, providing superior chip resistance and sharpness in high production, heavy-duty applications. That means higher cutting speeds, less interruption, and fewer tool changes, which translates to lower costs.
M42 steel is composed of 1.1% carbon, 3.9% chromium, 1.6% tungsten, 9.5% molybdenum, 1.2% vanadium, and 8.25% cobalt. Some of the most common uses for M42 steel are form tools, header tooling, punches, thread roll dies, twist drills, broaches, taps, milling cutters, reamers, end mills, and blades.
Since it can handle notoriously difficult to machine nonferrous superalloys, M42 is often used in manufacturing parts for oil, aerospace, and power generation sectors.
PM T15
This high speed steel shares the qualities of high wear resistance and impact toughness with M42 steel but is unique in that it has superior bend strength. This purple hardness, cobalt series steel grade is formed from clean steel with fine grain and small carbides.
Compared to lower alloy high speed steels, it offers a longer cutting tool life. PM T15 is an ideal choice for cold work tooling compared with high carbon, high chromium die steels.
Composition includes of 1.6% carbon, 4% chromium, 12.25% tungsten, 4.9% vanadium, and 5% cobalt. PM T15 is a popular choice for hobs, end mills, cut off blades, milling cutters, broaches, spade drills, tabs and form tools.